Comutador: O Coração Energético dos Motores de Tração – Princípios Estruturais, Desafios Técnicos e Análise de Aplicações
No sistema de operação do motor, o comutador, atuando como o “hub inteligente” que mantém a operação eficiente do motor, tem uma função central: garantir a saída de energia estável controlando de forma contínua e precisa a direção da corrente. Quando o motor é ligado, a escova forma uma conexão condutiva dinâmica com a superfície do comutador. À medida que o comutador gira em alta velocidade, seus segmentos de comutador (barras de cobre) fazem contato sequencial com a escova, convertendo a corrente contínua externa (DC) na corrente alternada (AC) necessária para o enrolamento. Esse processo é semelhante a uma “dança da corrente” precisa: o comutador alterna os caminhos da corrente em tempo real com base na posição rotacional do rotor. Por exemplo, quando o rotor atinge um ângulo específico, o comutador corta rapidamente a corrente no enrolamento atual e a redireciona para o próximo conjunto de enrolamentos, garantindo que os campos magnéticos do estator e do rotor mantenham sempre um ângulo ótimo de aproximadamente 90°. Isso gera um torque eletromagnético contínuo que faz o rotor girar sem parar. Sem esse controle preciso, a direção caótica da corrente causaria um desequilíbrio da força do campo magnético, arriscando o travamento do rotor, vibração ou até mesmo queima.
Como componente central dos motores de acionamento, o desempenho técnico e a qualidade do comutador ditam diretamente o desempenho geral do motor. Durante a operação em alta velocidade, o atrito frequente entre a escova e a superfície do comutador gera calor. Velocidades mais altas levam a temperaturas superficiais mais elevadas, o que pode aumentar a deformação radial do comutador e a deformação entre segmentos, elevar os níveis de faísca e, assim, encurtar a vida útil do motor. Portanto, seu projeto estrutural deve equilibrar condutividade elétrica, dissipação de calor e resistência ao desgaste.
As diversas estruturas dos comutadores plásticos são uma resposta direta aos requisitos acima mencionados, com parâmetros de projeto intimamente ligados à potência, tensão, velocidade e dimensões do motor. Atualmente, os comutadores semiplásticos convencionais geralmente consistem em uma carcaça plástica, segmentos do comutador (barras de cobre), isolamento de lâmina de mica e buchas metálicas. Essa combinação garante segurança através de materiais isolantes, assegura condução de corrente confiável por meio de componentes metálicos e utiliza uma carcaça plástica para construção leve e suporte estrutural – fornecendo uma base para otimizar o desempenho do motor em várias aplicações. Desde equipamentos industriais até eletrodomésticos, os comutadores permitem continuamente a operação eficiente do motor através de um projeto estrutural preciso e controle estável da corrente.
A figura mostra um diagrama esquemático da estrutura do comutador. Aqui, 1 representa o segmento do comutador, responsável pela comutação da corrente; 2 é a carcaça plástica, fornecendo proteção e suporte; 3 é a bucha metálica, garantindo a transmissão da corrente; e 4 é a lâmina de mica, servindo como isolamento para prevenir curtos-circuitos. Com este projeto estrutural, o comutador atende a múltiplos requisitos de desempenho para garantir uma operação eficiente e estável do motor.
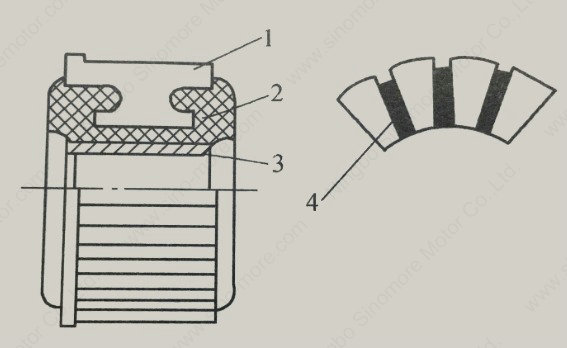
De acordo com a diferença na estrutura de conexão entre o segmento do comutador e a cabeça da bobina, os comutadores podem ser divididos em comutadores de ranhura e comutadores de gancho.
Para comutadores de ranhura, ranhuras são fresadas nas partes elevadas dos segmentos do comutador, e as cabeças das bobinas são embutidas nessas ranhuras, seguido pela tecnologia de soldagem por pontos (soldagem por pressão a quente). Durante o processo de soldagem por pontos, o filme de tinta do fio esmaltado é derretido pela alta temperatura, promovendo boas conexões elétricas entre as cabeças dos fios e entre as cabeças dos fios e as paredes das ranhuras do comutador.
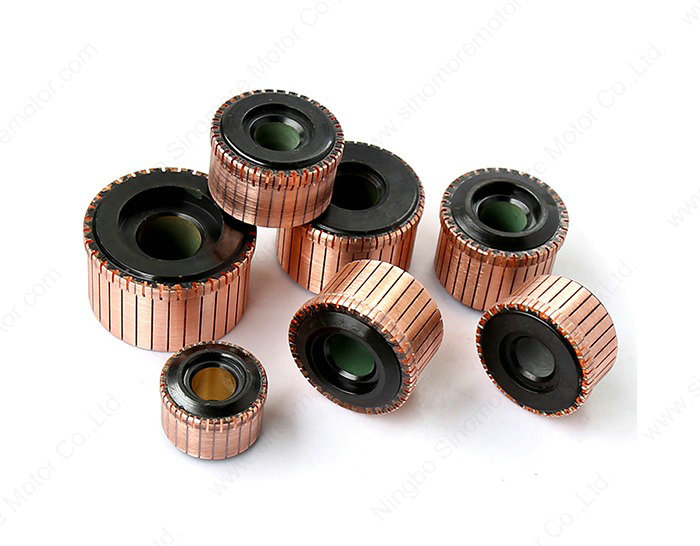
Este tipo de comutador facilita a automação do processo de conexão entre as extremidades da bobina e o comutador, mas é usado principalmente em cenários com menos segmentos de comutador e menor potência do motor. Isso ocorre porque motores de alta potência têm diâmetros de fio de bobina relativamente grossos, dificultando o enrolamento. Além disso, quando o número de segmentos do comutador é grande, a largura do gancho se estreita e as extremidades dos fios adjacentes são extremamente propensas a curto-circuitar.
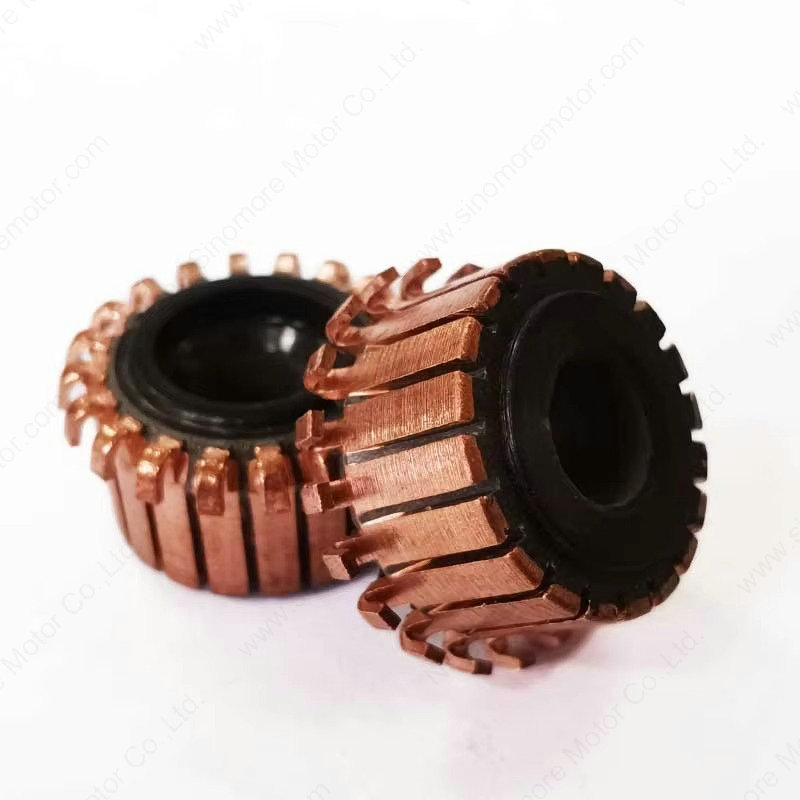
A carcaça do comutador é geralmente feita de plástico termoendurecível reforçado com fibra de vidro ou plástico de amianto. Como o comutador gera calor durante a operação e precisa suportar certas tensões mecânicas, os requisitos para a resistência ao calor e resistência mecânica do plástico são rigorosos. Ao mesmo tempo, seu coeficiente de expansão térmica também precisa ser o mais próximo possível do comutador de cobre. O pó de baquelite de resina fenólica é normalmente usado para atender a esses requisitos.
A principal função da bucha metálica é evitar que o plástico suporte tensões mecânicas quando o comutador é pressionado no eixo. No entanto, devido a limitações de tamanho, comutadores pequenos geralmente não possuem buchas metálicas. As buchas metálicas comuns incluem buchas de latão, buchas de mola e outros tipos.
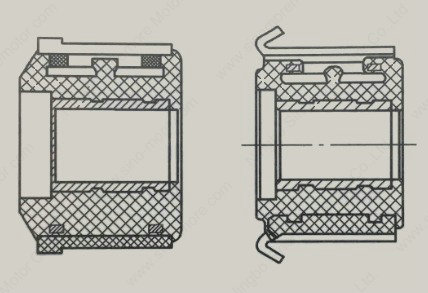
Lâminas de mica ou pó de mica são utilizados para isolação entre os segmentos do comutador. Devido à extrema resistência ao desgaste da mica, é necessário utilizar um processo de ranhuragem para deixar a lâmina de mica entre os segmentos mais baixa que a superfície dos segmentos do comutador, evitando assim que a resistente lâmina de mica sobressaia e afete o contato entre a escova e o segmento do comutador. Se a lâmina de mica sobressair, levará a uma queda no desempenho de comutação e poderá até causar falha no funcionamento normal do motor.
Os materiais das barras de cobre do comutador são divididos principalmente em duas categorias: uma é o cobre livre de oxigênio ou cobre eletrolítico, adequado para cenários com baixa velocidade de rotação, como motores de pequenos eletrodomésticos e arranques automotivos; a outra é a liga de cobre-prata, comumente usada em equipamentos como aspiradores de pó e ferramentas elétricas. Como a velocidade linear durante a comutação desses equipamentos é alta, a erosão por faísca pode causar o rápido aumento da temperatura superficial do comutador. O elemento prata adicionado na liga de cobre-prata pode melhorar a resistência à alta temperatura do material, tornar a superfície do comutador menos propensa a deformações e suprimir efetivamente defeitos como erosão por faísca e mau contato, garantindo assim operação estável em condições de alta velocidade.