Conmutador: El corazón energético de los motores de tracción – Principios estructurales, retos técnicos y análisis de aplicaciones
En el sistema de operación del motor, el conmutador, que actúa como el «centro inteligente» que mantiene el funcionamiento eficiente del motor, tiene una función central: garantizar una salida de energía estable al controlar de manera continua y precisa la dirección de la corriente. Cuando el motor arranca, la escobilla establece una conexión conductiva dinámica con la superficie del conmutador. Mientras el conmutador gira a alta velocidad, sus segmentos (barras de cobre) entran en contacto secuencial con la escobilla, convirtiendo la corriente continua (CC) externa en la corriente alterna (CA) requerida por el devanado. Este proceso es similar a un «baile de corriente» preciso: el conmutador cambia las rutas de corriente en tiempo real según la posición de rotación del rotor. Por ejemplo, cuando el rotor alcanza un ángulo específico, el conmutador corta rápidamente la corriente en el devanado actual y la redirige al siguiente conjunto de devanados, asegurando que los campos magnéticos del estator y el rotor mantengan siempre un ángulo óptimo de aproximadamente 90°. Esto genera un par electromagnético continuo que impulsa la rotación constante del rotor. Sin este control preciso, una dirección de corriente caótica causaría un desequilibrio en las fuerzas del campo magnético, arriesgando el bloqueo del rotor, vibraciones o incluso su quemado.
Como componente fundamental de los motores de accionamiento, el rendimiento técnico y la calidad del conmutador determinan directamente el rendimiento general del motor. Durante el funcionamiento a alta velocidad, la fricción frecuente entre la escobilla y la superficie del conmutador genera calor. Mayores velocidades provocan mayores temperaturas superficiales, lo que puede aumentar:
La deformación radial del conmutador
La deformación entre segmentos
Los niveles de chispa
Esto acorta la vida útil del motor. Por lo tanto, su diseño estructural debe equilibrar:
Conductividad eléctrica
Disipación de calor
Resistencia al desgaste
Las diversas estructuras de los conmutadores plásticos son una respuesta directa a los requisitos mencionados, con parámetros de diseño estrechamente vinculados a la potencia, voltaje, velocidad y dimensiones del motor. Actualmente, los conmutadores semiplásticos convencionales suelen constar de una carcasa plástica, segmentos del conmutador (barras de cobre), aislamiento de láminas de mica y casquillos metálicos. Esta combinación garantiza la seguridad mediante materiales aislantes, asegura una conducción de corriente confiable a través de componentes metálicos, y emplea una carcasa plástica para lograr construcción ligera y soporte estructural, sentando las bases para optimizar el rendimiento del motor en diversas aplicaciones. Desde equipos industriales hasta electrodomésticos, los conmutadores permiten continuamente un funcionamiento eficiente de los motores mediante diseños estructurales precisos y control estable de la corriente.
La figura muestra un diagrama esquemático de la estructura del conmutador. Aquí, 1 representa el segmento del conmutador, responsable de conmutar la corriente; 2 es la carcasa plástica, que proporciona protección y soporte; 3 es el casquillo metálico, que garantiza la transmisión de corriente; y 4 es la lámina de mica, que sirve como aislante para prevenir cortocircuitos. Con este diseño estructural, el conmutador cumple con múltiples requisitos de rendimiento para garantizar un funcionamiento eficiente y estable del motor.
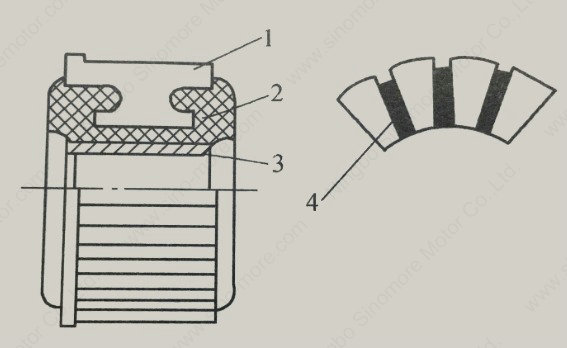
Según la diferencia en la estructura de conexión entre el segmento del conmutador y la cabeza de la bobina, los conmutadores se pueden dividir en:
Conmutadores de ranura (slot commutators)
Conmutadores de gancho (hook commutators)
Para los conmutadores de ranura, se fresan ranuras en las partes elevadas de los segmentos del conmutador, y las cabezas de las bobinas se insertan en estas ranuras, seguido de la tecnología de soldadura por puntos (soldadura por presión caliente). Durante el proceso de soldadura por puntos, la película de pintura del alambre esmaltado se funde por la alta temperatura, lo que promueve buenas conexiones eléctricas entre las cabezas de los cables y entre las cabezas de los cables y las paredes de las ranuras del conmutador.
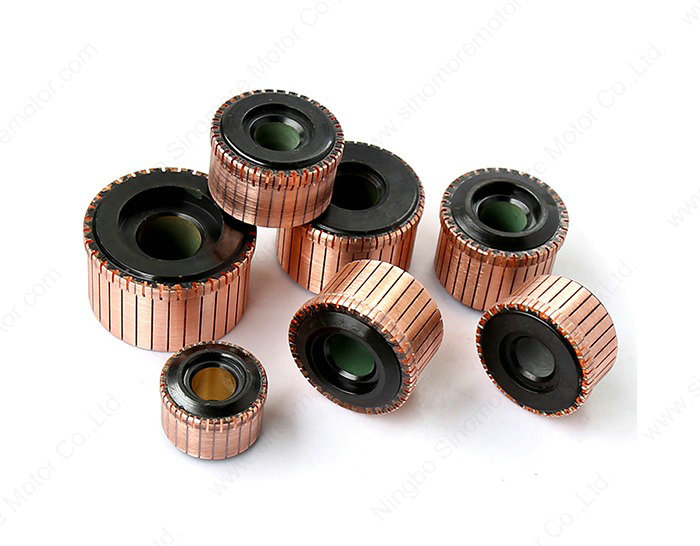
Este tipo de conmutador facilita la automatización del proceso de conexión entre los extremos de las bobinas y el conmutador, pero se utiliza principalmente en escenarios con menos segmentos de conmutador y menor potencia del motor. Esto se debe a que los motores de alta potencia tienen diámetros de cable de bobina relativamente gruesos, lo que dificulta el enrollado.
Además, cuando el número de segmentos del conmutador es grande, el ancho del gancho se reduce, y los extremos de los cables adyacentes son extremadamente propensos a causar cortocircuitos.
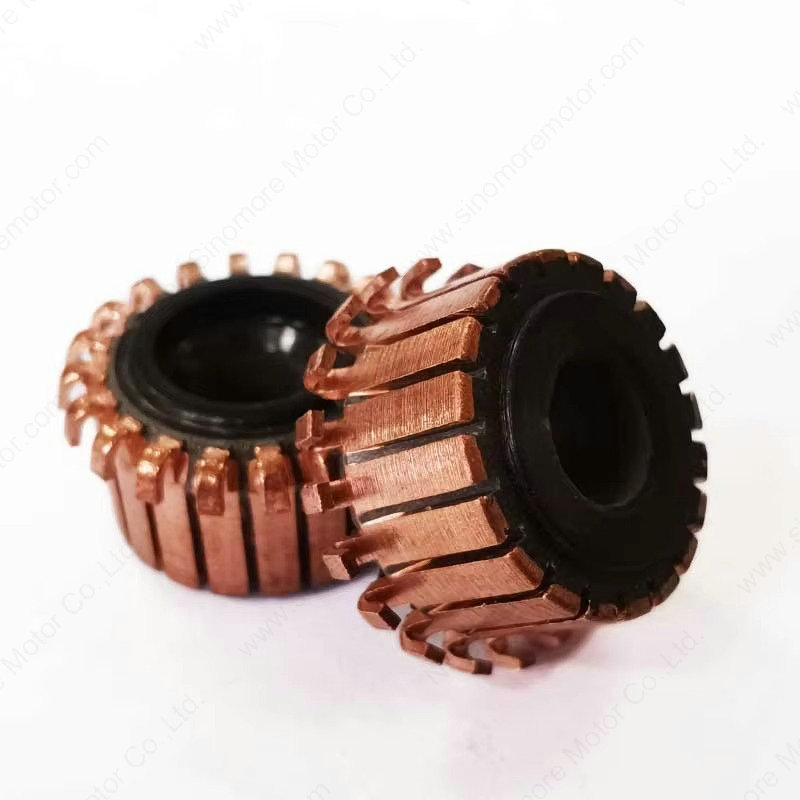
La carcasa del conmutador generalmente está fabricada de plástico termoendurecible reforzado con fibra de vidrio o plástico de asbesto. Dado que el conmutador genera calor durante su funcionamiento y debe soportar ciertos esfuerzos mecánicos, los requisitos de resistencia al calor y fuerza mecánica del plástico son estrictos. Simultáneamente, su coeficiente de expansión térmica también debe ser lo más cercano posible al del conmutador de cobre. Normalmente se utiliza polvo de baquelita de resina fenólica para cumplir con estos requisitos.
La función principal del casquillo metálico es evitar que el plástico soporte esfuerzos mecánicos cuando el conmutador se presiona sobre el eje. Sin embargo, debido a limitaciones de tamaño, los conmutadores pequeños frecuentemente no incorporan casquillos metálicos. Los casquillos metálicos comunes incluyen casquillos de latón, casquillos de resorte y otros tipos.
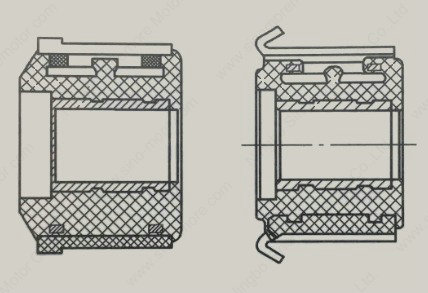
Se utilizan láminas de mica o polvo de mica para el aislamiento entre los segmentos del conmutador. Debido a la extrema resistencia al desgaste de la mica, es necesario emplear un proceso de ranurado para que la lámina de mica entre los segmentos quede por debajo de la superficie de los segmentos del conmutador. Esto evita que la resistente lámina de mica sobresalga y afecte el contacto entre la escobilla y el segmento del conmutador. Si la lámina de mica llegara a sobresalir, provocaría un deterioro del rendimiento de conmutación e incluso podría hacer que el motor dejara de funcionar correctamente.
Los materiales de las barras de cobre del conmutador se dividen principalmente en dos categorías:
Cobre libre de oxígeno o cobre electrolítico
Adecuado para escenarios con baja velocidad de rotación, como motores de pequeños electrodomésticos y arrancadores automotrices.
Aleación de cobre-plata
Comúnmente utilizada en equipos como aspiradoras y herramientas eléctricas.
En este tipo de equipos, la alta velocidad lineal durante la conmutación puede causar que la erosión por chispas eleve rápidamente la temperatura superficial del conmutador. El elemento plata agregado en la aleación de cobre-plata mejora la resistencia a altas temperaturas del material, evitando que la superficie del conmutador se deforme fácilmente. Esto suprime efectivamente defectos como:
Erosión por chispas
Malos contactos
Garantizando así un funcionamiento estable en condiciones de alta velocidad.